The Environmental Impact and Sustainability Measures in Bulk Ferro Alloy Manufacturing
Ferro alloys are essential components in various industries, ranging from steel production to aerospace. However, the manufacturing of ferro alloys comes with its fair share of environmental challenges. The extraction of raw materials and the energy-intensive processes involved contribute to greenhouse gas emissions, resource depletion, and other negative environmental impacts.
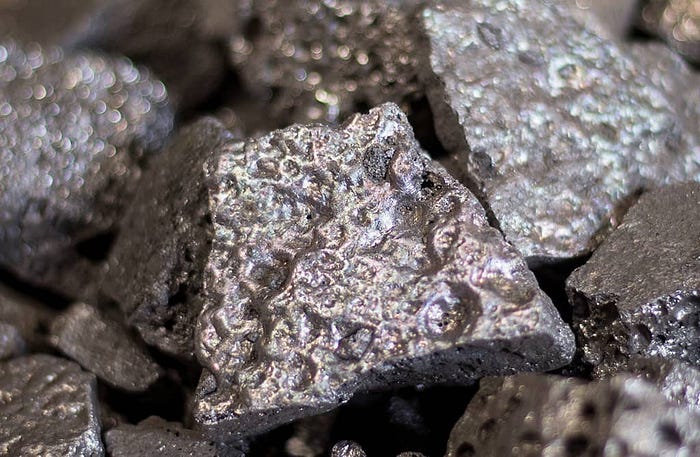
In recent years, there has been a growing emphasis on adopting sustainable practices within the ferro alloy companies like silico manganese manufacturers in India and other countries. This article explores the environmental impact of ferro alloy manufacturing and discusses key sustainability measures that can mitigate its effects.
Environmental Impact of Bulk Ferro Alloy Manufacturing
1. Resource Depletion: The production of ferro alloys requires significant amounts of raw materials, such as iron ore, manganese ore, chromium ore, and nickel ore. The extraction and processing of these ores can lead to habitat destruction, soil erosion, and water pollution, thereby impacting local ecosystems and biodiversity.
2. Energy Consumption: Ferro alloy manufacturing is energy-intensive due to high-temperature reduction processes involved in converting ores into ferro alloys. This results in substantial greenhouse gas emissions, contributing to global warming and climate change. Additionally, the reliance on fossil fuels for energy exacerbates these environmental concerns.
3. Air and Water Pollution: Emission of particulate matter, sulfur dioxide, and nitrogen oxides during the production of ferro alloys can lead to air pollution, affecting air quality and human health. Moreover, the wastewater generated in the process may contain heavy metals and other pollutants that can contaminate water bodies and harm aquatic life.
Sustainability Measures in Bulk Ferro Alloy Manufacturing
1. Material Efficiency: Adopting measures to increase the efficiency of raw material use can significantly reduce resource depletion. Recycling and reusing scrap metals and alloys can minimize the need for primary ore extraction. Implementing circular economy principles helps in reducing waste and conserving resources.
2. Energy Optimization: To address the energy-intensive nature of ferro alloy manufacturing, companies can invest in energy-efficient technologies. Transitioning to renewable energy sources, such as solar, wind, and hydroelectric power, can reduce greenhouse gas emissions and decrease the industry’s carbon footprint.
3. Emission Control: Installing advanced air pollution control technologies, such as scrubbers and filters, can mitigate the release of harmful emissions into the atmosphere. This not only improves air quality but also minimizes the negative health impacts on workers and nearby communities.
4. Water Management: Implementing efficient water management practices, such as treating and recycling wastewater, can prevent water pollution and minimize the consumption of freshwater resources. This approach also reduces the ecological impact on surrounding ecosystems.
5. Research and Innovation: Investing in research and development of cleaner production technologies and alternative raw materials can lead to more sustainable ferro alloy manufacturing processes. Breakthroughs in smelting methods and material substitution can significantly reduce environmental impacts.
While the production of ferro alloys has historically posed environmental challenges, the industry is now recognizing the importance of sustainable practices. By adopting measures to improve resource efficiency, optimize energy consumption, control emissions, manage water resources and promote research and innovation, manufacturing of bulk ferro alloys in India and abroad can transition towards a more sustainable and environmentally friendly future.
As global awareness of environmental issues grows, the ferro alloy industry’s commitment to sustainability will play a crucial role in reducing its impact on the planet.